Производство аккумуляторов высокого качества — это сложный процесс. Он основан на глубоком понимании электрохимии и включает точный подбор компонентов, создание настоящей ёмкости и, конечно, разработку надёжного корпуса.
В профессиональных сферах, таких как медицина, промышленность и геодезия, корпус даёт защиту от повреждений, влаги и агрессивных сред, гарантирует стабильную работу аккумулятора в сложных условиях.
Корпус делает аккумулятор съёмным, что упрощает обслуживание и хранение. Пользователь самостоятельно безопасно меняет батарею без сервисных центров и вызова специалистов. Тем самым владелец оборудования избегает простаивания и экономит деньги. Наличие запасных аккумуляторов помогает продлить работоспособность устройства, просто заменяя разряженный аккумулятор.
Neovolt 16 лет на рынке
Мы предлагаем аккумуляторы, которые соответствуют самым разным отраслевым стандартам. Нужен аккумулятор для работы в экстремальных условиях? Есть! Нужен аккумулятор с повышенной ёмкостью? Разработаем и изготовим!
Задумывались ли вы, как создается аккумулятор? Большинство компаний просто закупают готовые корпуса в Китае. Neovolt делает их самостоятельно здесь в России в Москве — от 3D-модели к прототипу и до готового изделия.
Хотите узнать, как рождается корпус аккумулятора? Тогда читайте дальше! Мы расскажем обо всех этапах.
Этап 1. Проектирование и моделирование
Всё начинается с технического задания: чертежа или описания требований.
Пример
Заказчик прислал техническое задание на аккумуляторную батарею специфической формы под собственное оборудование для внутритрубной диагностики (газо- и нефтепроводы).
- 1.1. Проектирование
Инженер должен превратить техзадание в рабочий проект. Разделить на этапы (моделирование → 3д печать → проверка размеров и сборки → литьё → прототип → тестирование → внедрение в серию → производство).
- 1.2. Расчёт
Количество элементов, тип и размеры, проверка доступности компонентов.
- 1.3. Моделирование
Визуализация с помощью специализированного ПО Solidworks, где учитываем:- • исходный чертеж,
- • расположения элементов,
- • толщины стенок для отливки (изготовление слишком тонких или сложных форм может быть технологически сложно или невозможно).
- 1.4. Спецификация
Документация включает:- • компоненты и этапы — для отдела закупок, для управляющего производством (распределяет заказы в очереди) и монтажника (сборка);
- • инструкция для сборки;
- • другие указания для соответствия номинальным характеристикам и требованиям безопасности.
Подбор компонентов и проектирование — сложная задача. Она требует учёта множества факторов, включая ёмкость, ток, габариты, условия эксплуатации, обеспечить нужными защитами и всё это при ограниченном месте в корпусе.
В результате получаем цифровой двойник будущего аккумулятора. Модель готова к производству.
Этап 2. 3D-печать прототипа
После завершения проектирования создаётся физический прототип корпуса. Это делается с помощью 3D-печати. Прототип служит мастер-моделью для последующего литья в силиконовую форму.
Цель этапа
Создание физического прототипа корпуса для последующего литья в силиконовую форму.
- 2.1. Модель готовим к печати
Добавляем поддержки — специальные элементы, необходимые для печати навесных деталей. Выбираем параметры печати, оптимальные для выбранной смолы.
- 2.2. Выбираем материал
Инженер использует специальную смолу, совместимую с платиновым силиконом, из которого будет изготавливаться форма. В приоритете точность и качество литья.
Комментарий инженера:
«Добавляем поддержки и параметры печати для конкретной смолы в зависимости от задач для отливки в платиновый силикон».
Таким образом, получен прототип корпуса, напечатанный на 3D-принтере. Ему предстоит пройти большой путь, прежде чем стать мастер-моделью с созданием формы, оценкой дизайна, эргономики и выявлением потенциальных проблем до начала литья.
Этап 3. Изготовление формы: создание основы для будущего корпуса
Напечатанный на 3D-принтере прототип — это только начало. Теперь сосредоточимся на форме для литья. Именно в ней рождается корпус будущего аккумулятора. Использование платинового силикона для изготовления форм гарантирует высокую точность и детализацию.
- 3.1. Подготовка прототипа
Обрабатываем поверхность прототипа, чтобы обеспечить идеальное прилегание силикона и получить гладкую, ровную форму.
- 3.2. Заливка силиконом
До заливки устанавливаются литники для последующей заливки пластика и выхода воздуха; создаётся опалубка для формы; заливается силикон.
- 3.3. Дегазация
Помещаем форму в вакуумную камеру для удаления воздуха из силикона. Этот процесс, называемый дегазацией, критически важен для получения качественной формы без дефектов.
Комментарий инженера:
«Всё начинается с создания формы, это долгий процесс; сначала подготовка образца; заливка силиконом с дегазацией; результат — форма с деталью».
Получаем готовую силиконовую форму. С её помощью будет изготовлено множество идентичных корпусов аккумуляторов с высокой точностью. Теперь подробно остановимся на литейном производстве корпусов.
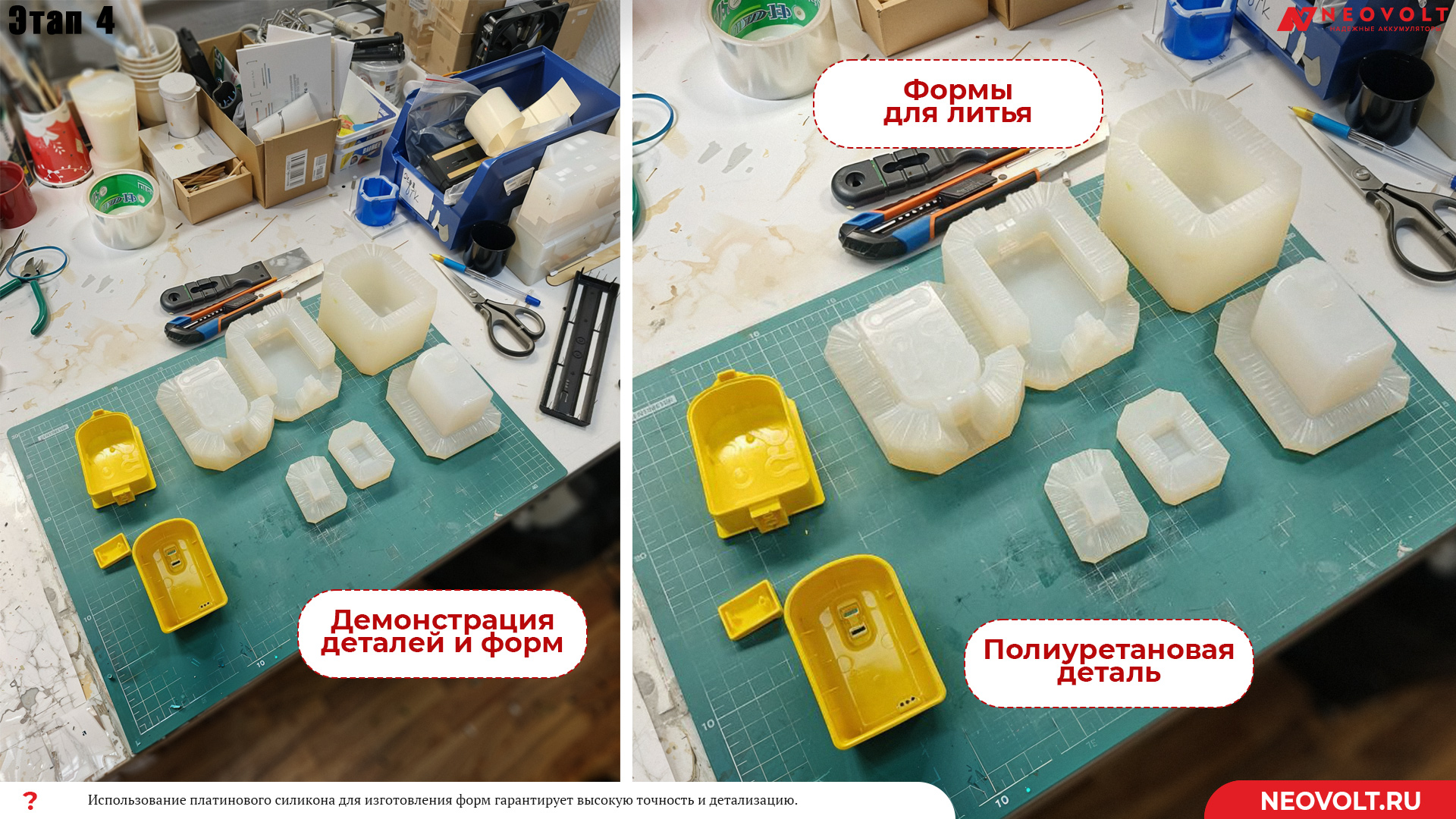
Этап 4. Литьё корпуса: от формы к готовому изделию
Получив форму, мы приступаем к непосредственному литью корпуса аккумулятора. Используем двухкомпонентный полиуретан.
Двухкомпонентный полиуретан
Это система холодного отверждения, состоящая из двух жидких компонентов, которые при смешивании образуют прочный, гибкий и износостойкий пластик. Материал идеально подходит для литейных процессов при создании корпуса аккумулятора по прочности, лёгкости и химической стойкости при заданной спецификацией толщине.
Итак, у нас есть форма, и мы хотим получить деталь. Берём специально подготовленный жидкий полиуретан — он состоит из двух компонентов, которые мы предварительно смешали. Аккуратно заливаем его в форму.
Но просто залить недостаточно. Внутри могут остаться пузырьки воздуха, которые испортят деталь. Чтобы избавиться от них, помещаем форму с полиуретаном в вакуумную камеру — это называется дегазация.
Как только воздух удалён, отправляем форму в специальную печь. Там под воздействием температуры полиуретан затвердевает — этот процесс называется полимеризация.
Когда деталь готова, достаём её из формы, обрезаем лишние кусочки пластика, которые называются литниками. Теперь корпус аккумулятора практически готов. Осталось его подшлифовать и придать товарный вид.
Вот, как процесс выглядит поэтапно:
- 4.1. Заливка и дегазация
Тщательно смешиваем компоненты полиуретана в точных пропорциях для достижения нужных свойств материала, заливаем смесь в подготовленную силиконовую форму и помещаем её в вакуумную камеру для дегазации,чтобы удалить воздух из полиуретана и избежать образования пузырьков в готовом корпусе.
- 4.2. Полимеризация
Помещаем форму с полиуретаном в печь для завершения процесса полимеризации — затвердевания материала (температурный режим и время полимеризации строго контролируются).
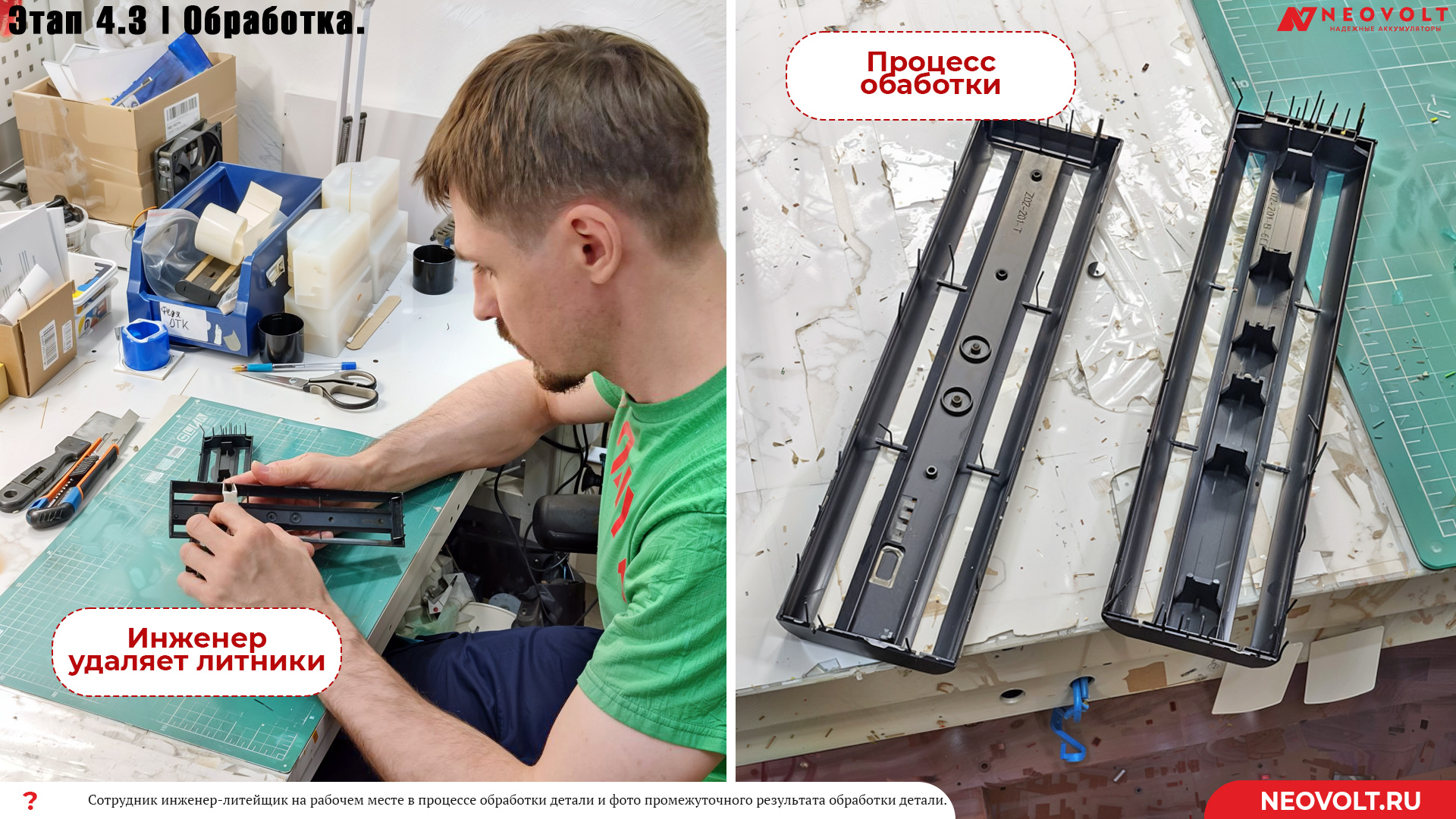
- 4.3. Обработка
После остывания извлекаем корпус из формы и удаляем литники — излишки материала, образовавшиеся в местах заливки.
Для придания корпусу идеальной формы и гладкости проводится шлифовка и другая необходимая обработка. Получаем готовый корпус аккумулятора, обладающий требуемыми спецификацией механическими и химическими свойствами.
Этап 5. Покраска и покрытие: защита и эстетика
После литья и обработки корпус аккумулятора практически готов. При необходимости мы проводим покраску и нанесение специальных покрытий.
- 5.1. Подбор цвета
В ряде моделей требуется подобрать цвет по желанию заказчика или в соответствии с фирменным стилем.
- 5.2. Покраска
Наносим специальную износостойкую краску, которая не боится ни царапин, ни ультрафиолета, ни агрессивных сред.
- 5.3. Сушка
Чтобы краска хорошо закрепилась, корпус отправляется в сушильную камеру.
- 5.4. Нанесение защитного покрытия (опционально)
Для ещё большей защиты можно нанести специальный лак, который делает корпус практически неуязвимым. А если аккумулятору предстоит работать в экстремальных условиях, где важна герметичность, то добавляем герметики, уплотнители и специальные разъёмы с заглушками, чтобы он соответствовал стандартам защиты IP67 или даже IP68. Это значит, что ему не страшны ни пыль, ни погружение в воду.
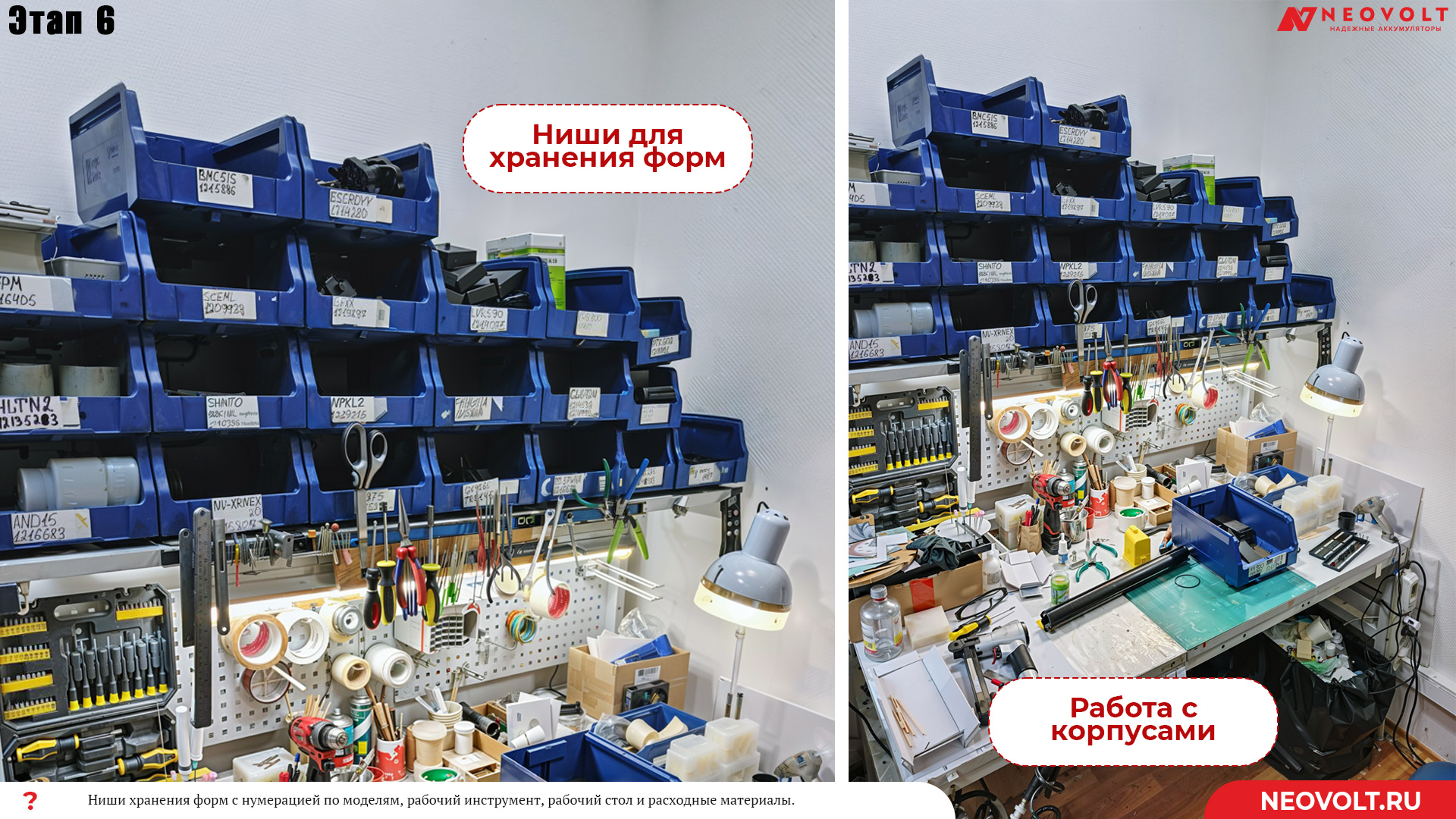
Этап 6. Ускорение выполнения заказов
Силиконовые формы имеют ограниченный срок службы и со временем изнашиваются. Для востребованных и популярных моделей создаётся несколько экземпляров форм.
Комментарий инженера:
«Инженер-литейщик применяет множество форм в своей работе. Наиболее часто используемые всегда находятся на рабочем месте литейщика в нескольких экземплярах. Форм обычно в 2-3 раза больше, чем требуется, так как со временем они твердеют и постоянно нужно делать новые».
Так мы снижаем риски задержек в производстве. Формы хранятся в специальном хранилище с организованной системой каталогизации. Самые ходовые всегда доступны на рабочем месте инженера-литейщика.
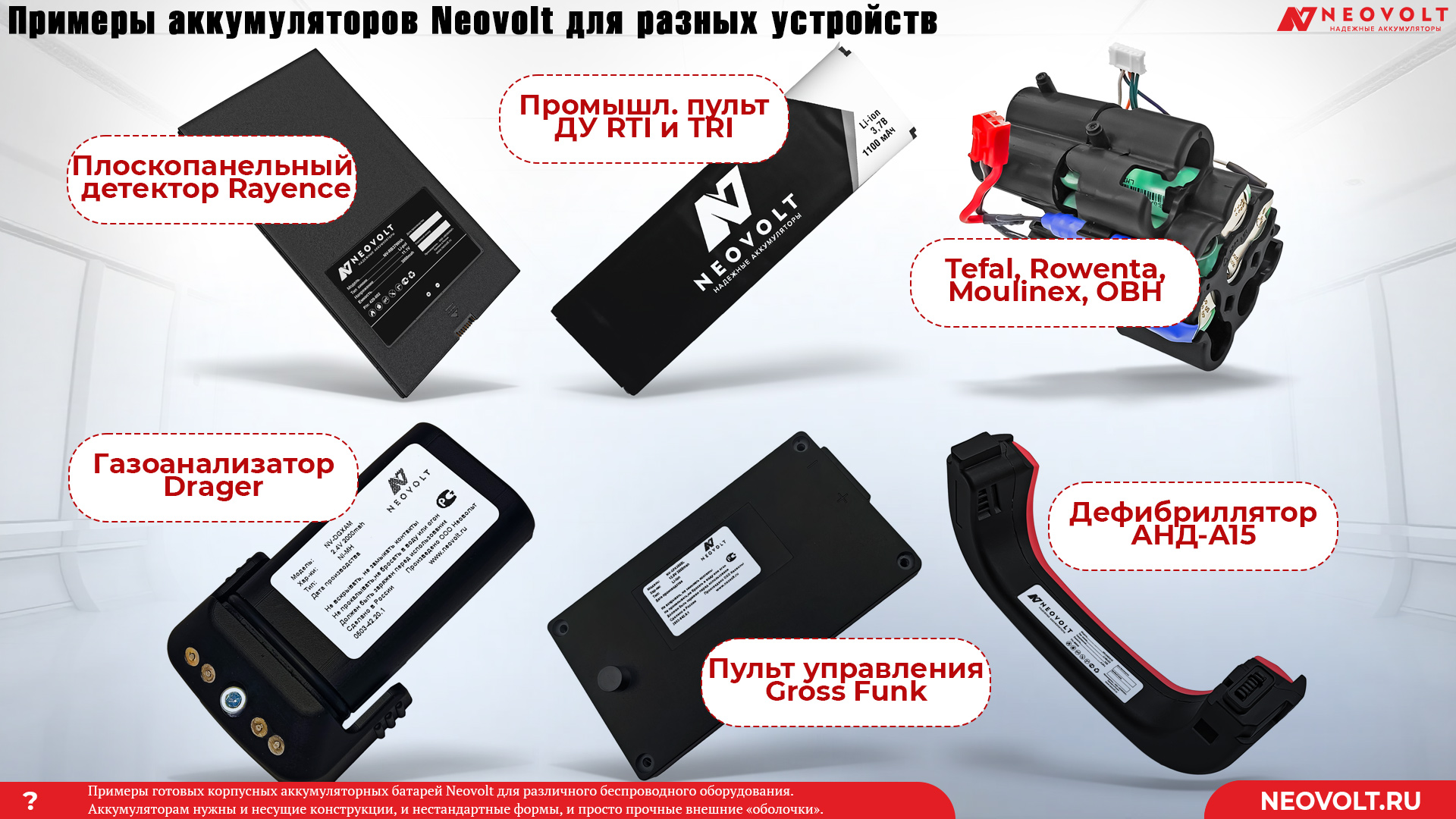
Заключение и выводы
Создать по-настоящему хороший аккумулятор — непростая задача. Это путешествие от идеи до готового продукта, где каждый этап требует точности, современного оборудования и опытных специалистов. В Neovolt мы контролируем весь процесс — от первого эскиза в CAD-системах до финального штриха.
Благодаря собственному производству наши инженеры берутся за нестандартные проекты и быстро реагируют на пожелания заказчиков.
Мы не штампуем аккумуляторы как китайские производители — лишь бы продать. Нас волнует, будет ли продукт работать у вас долго и эффективно.
Хотите узнать больше или заказать аккумулятор, даже если он редкий или снят с производства? Заполните форму для заказа:
Выбирая Neovolt, вы получаете надёжное и долговечное решение. Закажите аккумулятор Neovolt уже сегодня — он разработан и произведён специально для вашего оборудования.